Prefab housing is on the rise, due to a variety of factors including labor and material shortages, and let’s face it, the need for more affordable housing. Mordor Intelligence suggests prefabricated housing will top at least $143.55 billion by the end of 2025 and it will soar to $198.25 billion by 2030, which is a 6.67% growth rate. I think even the Queen of Prefab would approve these numbers!
The U.S. Census Bureau estimates there are roughly 7 million prefabricated homes in the United States, which represents about 7.5% of all single-family homes. Also, more than 80% of contractors have already embraced off-site building techniques like modularization.
The trend is really picking up speed, especially since traditional homebuilding methods require roughly seven months from groundbreaking to completion. This is challenging with labor shortages, weather delays, and rising material costs.
Let’s look at one example of prefab. In 2017, father-son duo Paolo and Galiano Tiramani began researching and testing materials and methods that would enable the automotive-style mass production of houses, and BOXABL was born.
BOXABL’s primary innovation is its patented folding building system that enables efficient factory production and achievable transportation logistics. With its methods and technology, it can produce a complete home every four hours. This is significantly faster than the seven months for conventional construction.
Other advantages include being able to eliminate weather-related delays since it is built in a factory environment, and standardized components enable economies of scale. Also, vertical integration of manufacturing processes reduces supply-chain vulnerabilities and automated production reduces labor dependency.
BOXABL designed and produced the first few prototypes of the Casita and showcased it at the Intl. Builders’ Show in 2019. At 361-sq.ft., the Casita model has complete fixtures and utilities for roughly $60,000.
In May 2021, BOXABL received a federal contract worth more than $9,000,000 to build and deliver 156 Casitas for use at a military base. That same year, BOXABL broke ground on its first factory in Las Vegas, Nev. The following year, BOXABL partnered with homebuilder DR Horton, which included an order for 100 Casitas. In 2023, BOXABL built second and third factory buildings.
Today, BOXABL also has Baby Box, which is a 120-sq-ft living space built to the RV code. The company is also expanding the product line to allow customers to stack or connect Boxes to build different building types including single family dwellings, townhouses, and apartment homes.
Looking to the future, BOXABL is currently in the planning stages for the next step—a multimillion square foot factory, which it is calling the BOXZILLA Factory. This factory would house advanced automation equipment.
Of course, this is only one example. We have seen other cases of homebuilders focusing on prefab construction. For instance, we have written about Clayton’s CrossMod homes, which combines off-site construction with site-built features. We have also covered Mighty Buildings, which is a 3D printing company that is opening a factory to print climate-resilient homes for the U.S. market.
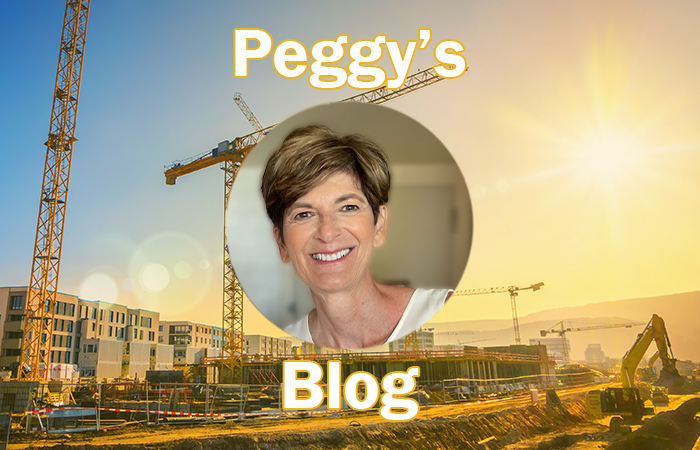
Prefab is a trend that is picking up speed both in residential and commercial construction, offering opportunities to build more affordable housing with a smaller workforce. It will certainly be a trend to continue to watch in the days ahead.
Want to tweet about this article? Use hashtags #construction #IoT #sustainability #AI #5G #cloud #edge #futureofwork #infrastructure #prefab