Autonomous vehicles, self-driving cars for example, are in the news a lot lately, not always in a positive way. San Francisco, which was a pioneer testbed for them has pulled some of them off the streets. Cruise, a division of General Motors, and Waymo, a subsidiary of Google’s parent company Alphabet, have been running robo-taxis on the streets of San Francisco for several years.
Cruise and Waymo expanded operations to all the city in 2023 with Cruise claiming 300 autonomous cars running during the day and 100 at night; Waymo had 250 cars on the streets. But in August the California DMV ordered Cruise to cut its fleet in half after a series of accidents and intersection blocking events. By October 24, the DMV suspended Cruise’s license to operate the cars without a safety driver present. Cruise could continue to deploy vehicles with a safety driver on board but couldn’t charge fares. On November 16, Cruise paused all operations nationwide; the only active Cruise cars now operate on “closed course training environments.”
Waymo continues to operate in a slightly restricted manner in The City—local speak for San Francisco—and the legal battles continue. But the main reason there are battles is the vehicles operate throughout the city streets, a naturally wild environment. As the saying goes, anything goes in the city. Pedestrians crossing between parked cars? Naturally. Dogs running after squirrels across the street? Normal day. Heavy trucks entering the street from construction sites? All too common. Autonomous cars avoiding these obstacles? Not always.
Digging In
Other companies are taking a different path. The types of autonomous vehicles that can be operated within an enclosed setting, such as vehicles used on construction sites, will gain acceptance before self-driving cars do. By confining the vehicles to a geo-fenced area, safety concerns are minimized and data on performance and reliability are easily obtained.
Built Robotics, ironically a San Francisco company, is equipping construction equipment with technology currently employed in industrial robotics to create autonomous vehicles. The vehicles can do work that is dangerous, repetitive, or both, with very little human intervention. Built Robotics introduced its ATL (autonomous track loader) for digging and grading in large, well-defined areas, such as foundations, back in 2017. Using LIDAR sensors, IMUs (inertial measurement units), and GPS (global positioning system) technology, location-sensing can be determined down to the centimeter. The ATL can therefore handle basic construction site tasks, such as digging foundation holes and trenches.
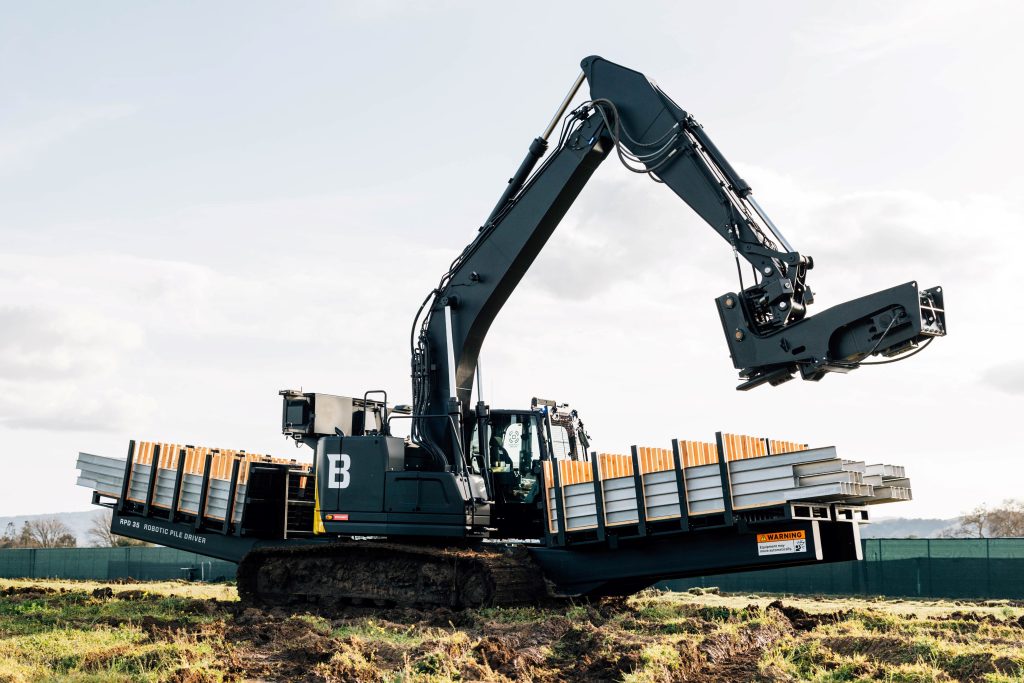
The “programming” is more like giving instructions to a worker than to a robot. Instead of details, goals are set, and all the path planning, progress monitoring, and decision making are completed autonomously. A geofence for the jobsite is laid out by a human worker and the machine is given goal parameters—where to dig, where to place the dirt that has been excavated, where to avoid—and the vehicle will operate autonomously within those parameters.
The ATL and other autonomous construction vehicles are designed to address key issues in the construction industry, including a shortage of skilled labor, a desire to increase efficiency on the jobsite, and demand for enhanced worker safety. Sending an autonomous piece of equipment to do a dangerous job, when it can do that job, relieves a human worker of that danger. And that includes repetitive work that can be boring, leading to distraction and injury or operator error.
The ATL is particularly suited for handling simple tasks, but humans are still required to manage and complete more complex jobs, such as excavating around buried utility lines, fine grading of work sites, and loading trucks. Taking its experience with autonomous trenching and digging, Built adopted its control system to other manufacturer’s excavators, creating the Exosystem. Adding the Exosystem to an excavator creates an autonomous piece of equipment.
Built leases a kit that adds autonomous robotic capabilities to existing construction equipment with a combination of cameras, GPS, and artificial intelligence. This robotic platform can be installed on machinery from Caterpillar, Hitachi, John Deere, and Volvo as an aftermarket upgrade, according to the company.
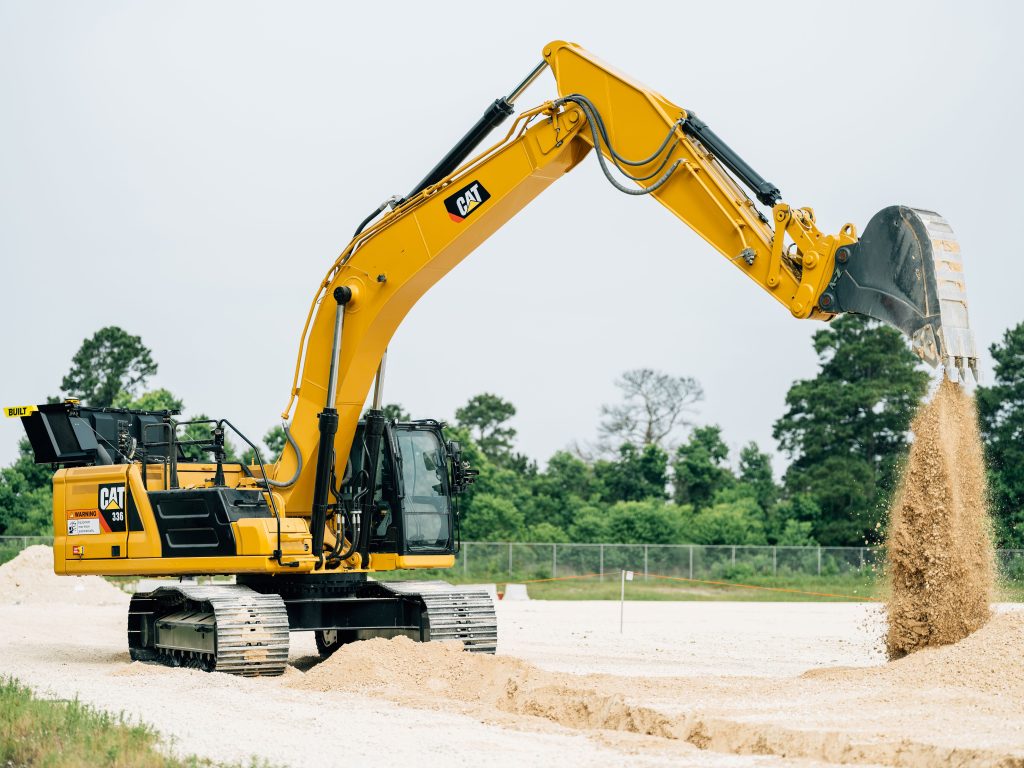
Analyzing its market, Built has moved its technology to a more focused approach, and that focus is on solar farms. The RPD-35 robotic pile driver is an autonomous piece of equipment designed to speed the construction of utility scale solar farms.
Loading Up
In some environments, even loading trucks can be automated. A mine site is an ideal environment for autonomous vehicles. Haul trucks travel predictable routes at predictable speeds. They go from fixed point to fixed point, and autonomous machines are immune to the fatigue and distraction faced by human operators who spend hours at the wheel performing a monotonous task.
While a human operator can get bored and have an accident, autonomous equipment is also subject to making mistakes. Even if the route is repeated and programmed, everything and everyone else on the site is not. Just like in the city, other machines, light vehicles, personnel on foot, loose debris, and more might end up in the path of an autonomous truck.
Being able to detect and react to surrounding conditions and obstacles is critical to the safety and productivity of an autonomous system. For a human operator, if you see another vehicle approaching an intersection, you apply the brakes and, depending on priority rules at that site, wait until the obstacle or vehicle is clear, and then resume driving.
For an autonomous vehicle? How does a truck with no driver see what’s coming and know how to react? Caterpillar has an answer, Cat’s MineStar Command for hauling. This acts as the truck’s perception system, based on LiDAR. In practical terms, LiDAR is a RADAR variation that uses light waves instead of radio waves for detection of obstacles. A similar system is adopted to the autonomous cars in San Francisco and other cities.
Autonomy is rapidly emerging in the mining industry as essential for improving safety, productivity, and lowering costs. Equipment equipped with Command enables total autonomous operating of the mining trucks, interaction with other equipment, and integration with customer mining processes and systems, all managed by MineStar.
Since the Cat 794 AC electric drive truck debuted in 2016, the global fleet has logged more than 780,000 hours of field operation, averaging a physical availability of 90%. In 2021, the Cat 794 AC became the latest autonomous mining truck equipped with Cat MineStar Command for hauling. It is the first electric drive model to join the expanding autonomous haulage fleet.
Demonstrating up to a 30% productivity improvement over operator-driven models at mine sites, MineStar Command addresses mining challenges including labor shortages and the demand for higher machine utilization. Autonomous trucks surpassed 3-billion tons hauled with no lost-time injuries associated with automated truck operation, enhancing safety.
Want to tweet about this article? Use hashtags #construction #sustainability #infrastructure #IoT #cloud #edge